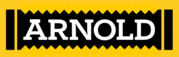
Arno Arnold GmbH
Über uns
1864
The company’s history began in 1864 with Ernst Louis Arnold, who founded ELA and directed the company together with his three sons in Carlsfeld in the German region of the Erzgebirge.
1890
The early days of Arnold were inseparably connected with the tango – the music that stands for pure erotic, turning shy people into Latin lovers. Tango is not only a dance but a celebration.
This is not astonishing at all because tango had been established in the brothels of Argentine around 1890. It became a fashionable dance for everybody in Paris and soon spread all over the world.
There was one instrument being very essential in the creation of the typical tango sound – the bandonion which was developed just by rebuilding the concertina. Heinrich Band, a music teacher, had the idea in the German city of Krefeld some 150 years ago. The Arnold brothers – Alfred and Paul – from the city of Carlsfeld made the instrument world-famous. After World War I, Paul Arnold’s son Arno started producing bandonions in the city of Obertshausen.
1910
After ELA ceased to exist, one of his sons, Alfred Arnold, founded the company in 1910. His brother Wilhelm Paul Arnold participated in the company and let his son Arno Arnold take part in the enterprise. Arno Arnold became the only managing director in 1933.
The bandonion belongs to the group of instruments with bellows. By pulling and pushing, currents of air are produced and later transformed into tones with the help of a keyboard. Heinrich Band’s innovation was more successful than the concertina. This is not only due to its tone but also to the fact that it has a wider range of tones. The so-called standard bandonion already had a range of 144 tones in 1924. This was the development from a manageable instrument that offered many technical possibilities in the classical sense to the "absolutely perfect hand instrument”, as described by enthusiastic experts.
1930
Alfred Arnold was granted the patent "harmonica-shaped bellows used for covering the guide ways at machine tools, especially for covering the sled guide way at grinding machines” by the patent office in Carlsfeld in 1930.
By taking an amateurish look at the design drawings, the bandonion mechanics become obvious. Bellows became the second important product after the world-famous "AA” bandonions. The production of bandonions further increased. In order to accelerate the flow of work, Arnold wrote in his essay "What kind of tools are needed for the first steps?”: a 3-locker drill to avoid changing the drills during work.
1949
The Federal Republic of Germany was established in 1949 and Arno Arnold was encouraged to make a new start in the city of Obertshausen. His reasons for settling there might have been the skilful local workers producing leather goods, the raw material leather itself or just personal motivation. Anyway, Arno Arnold did not get any properties or subsidies from the community. The commercial risk was enormous but Mr. Arnold was rewarded some years later. At that time, the production of bandonions still played an important role in the "new” Arno Arnold GmbH, but a change was going to come soon.
The company kept up with the recovering of the German economy and concentrated more and more on the further development of covers.
1955
The gradual but decisive step from music to machinery was made when Günter Weinmann and his wife Sigrid Weinmann, née Arnold, joined the company. He founded the company Weinmann Faltenbälge GmbH, which developed the original WMB spiral, a conic spring spiral for protecting spindles in shafts and was granted a patent for the manufacturing procedure in many European countries. The manufacture of protective devices for gliding channels and bellows cameras was becoming more and more the focus of the company’s activities.
1971
The last bandonion was finally produced in 1971. Nevertheless, the company’s traditional duty to produce superior products that fully satisfy the clients has never been rejected.
1984
When management of the company was taken over by Arno Arnold’s granddaughter Simone Weinmann-Mang and her husband Wolf Matthias Mang, the two companies Weinmann Faltenbälge and Arno Arnold merged in the eighties to become ARNO ARNOLD GMBH – an international partner for protective and safety systems.
2000
Until today, Arnold’s products have a very good reputation world-wide. The company’s principles, for example quality, customer-orientation and service, have become a standard for a whole branch of industry.
In addition to that, TÜV Hessen under the registration no. 73 100 508 has certified us in accordance with DIN EN ISO 9001 in 1998 to develop, produce and market protective systems. Furthermore, our production facility is certified by TÜV PRODUCT SERVICE which guarantees a faultless and consistent production quality.
2001
The year 2001 again has seen interest in our products increase. At the beginning of the year we have almost doubled our production space in Oberhausen.
Arno Arnold's past has been eventful and groundbreaking and our future will be innovative and successful.
Your competent partner for protective systems.
2004
Certified in accordance with the new version of the standard DIN EN ISO 9001: 2001; certification extended until 2007.
In the last three years, application has been made for several more interesting patents and patterns. The principle of “rear tensioning elements” represents a completely new principle for increased contact pressure of the telescopic sheets in the working area. This promising development, together with the new products “Fix & Finish” and “WINGS” demonstrate the innovative powers and strength of the ARNOLD company, which are also impressively confirmed by the registration of over 35 patents, patterns and proprietary rights over the last 15 years.
2005
Once again this year we have been able to offer our customers a host of new innovations.
True to our EMO 2005 exhibition motto "Vision is possible", we presented 5 new developments to visitors to our stand: The Patent applications
CURVELET: A neat solution for the corner
WINGLET: A wing ensures contact pressure
TOPCLOSE: A robust, lightweight chain-link cover
DETECTA: A brand-new cover - detects damage to laser beam guide bellows
SLIMCOVER: The cover with minimum space requirements
2006
ARNOLD continues to grow and grow and grow …
With an increase in order intake of over 20%, we have continued on our expansion course. With the acquisition of around 1,400 m2 of production and warehouse area, and the establishment of a Technology and Trials Centre, we are now able to fulfil customer needs and requirements more quickly and efficiently.
ARNO ARNOLD is therefore operationally and strategically well-equipped for the challenges of the future.
Arno Arnold had an exciting, pioneering, successful and innovative past and definitely, the future will be just like this, according to the motto - "future by origin”.
2007
At the EMO 2007 in Hannover, ARNO ARNOLD presented innovations "for more movement in the market". The new products allow even more flexibility and independence in their application.
In order to help our customers with an optimisation of their inventories, we have established a new automatic warehouse.
Thus, as a selected supplier, we can ensure for our customers a materials planning process according to JIT/JIS or the kanban system.
2008
A "supporting" role was played by one of the innovations that ARNO ARNOLD presented at the AMB 2008 in Stuttgart. Catena, a self-supporting element with a "steep" flexibility.
Unsere Werte
The Team
Being together is decisive, that’s why we place great emphasis on teamwork and know that one person alone is only in control of his part. It is only together that things are realized really successfully. The quest to always achieve better results is an obligation for everyone who is part of our company. The will to achieve something exceptional is, for our employees, an attitude as well as a duty. Our engineers view tasks which appear to have no solution as a special challenge which they tackle with dedication.
We guarantee that our protective cover systems meet the highest demands. Using sophisticated durability tests and specific simulation procedures, we examine, in our test centre, the materials, flexibility, robustness and operation speeds under extreme conditions. We, and of course our customers can therefore be sure that our protective cover systems meet the high demands placed on them in the long-term.
“Made in Germany” is, and remains, a label associated with a high quality standard and reliability and with which German products have made a name for themselves worldwide.
The great care with which we produce our protective cover systems has brought us the reputation of being a business with an exceptionally high level in manufacturing.
Sustainable economic operation with limited resources is, as a responsible business, an important concern and responsibility of ours.
We use the latest production systems and our staff handle materials and machines responsibly. In this way, products are produced which fully do justice, in every way, to the label “Made in Germany”.